Chemicals
Success Stories.
What results will I see from Osprey’s products and services? What sort of return on investment can I expect in comparison to other options? How does it work? Our short, easy-read case studies will answer all of those questions and more. We’ve driven real results for our clients in the Chemicals industries. Find out how we use our approach to make your systems more effective, affordable and sustainable:
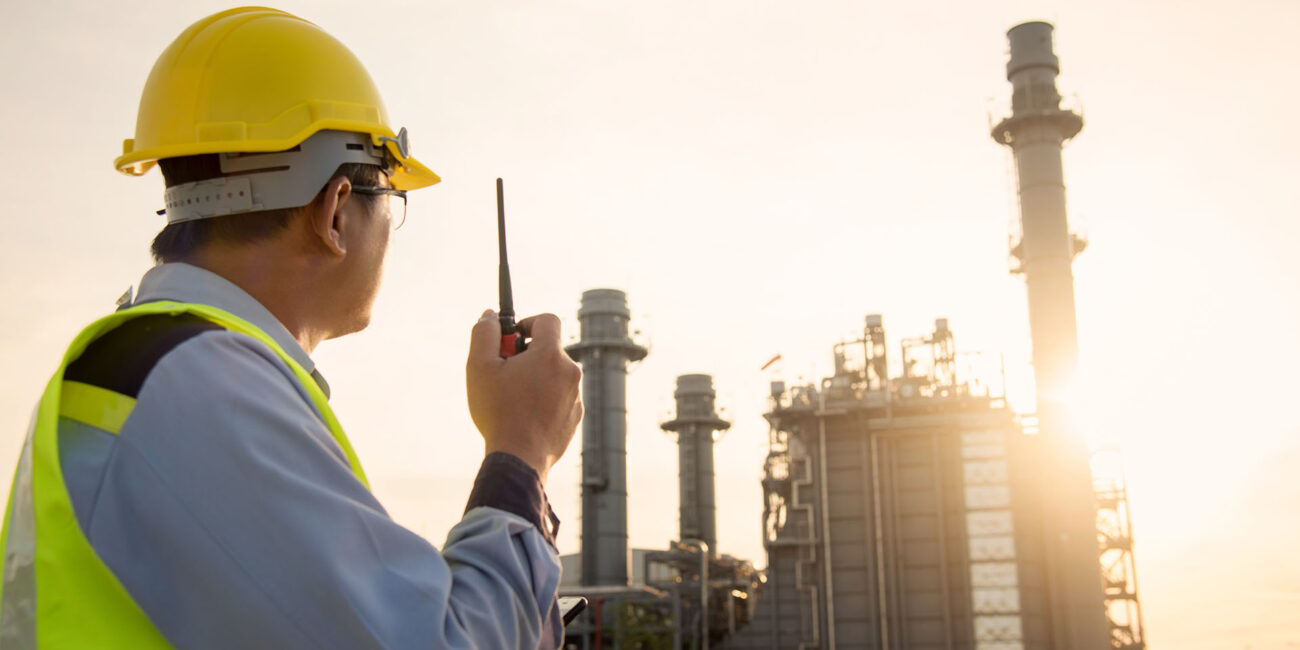
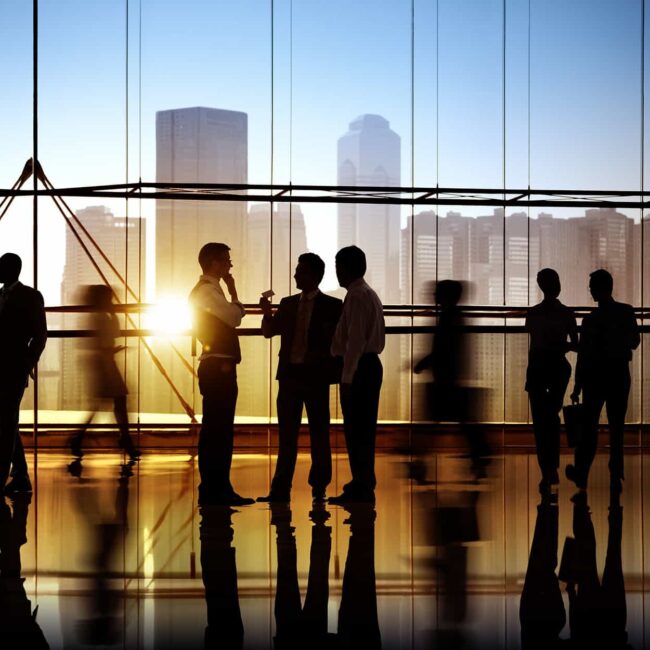
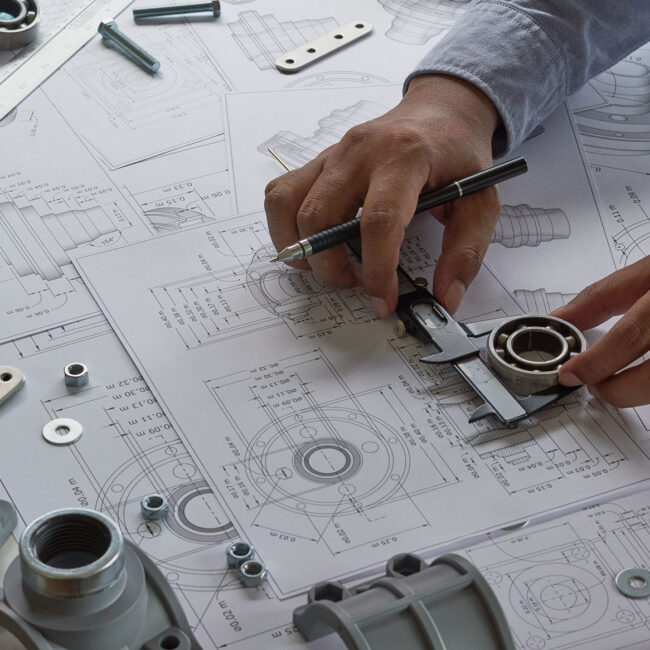
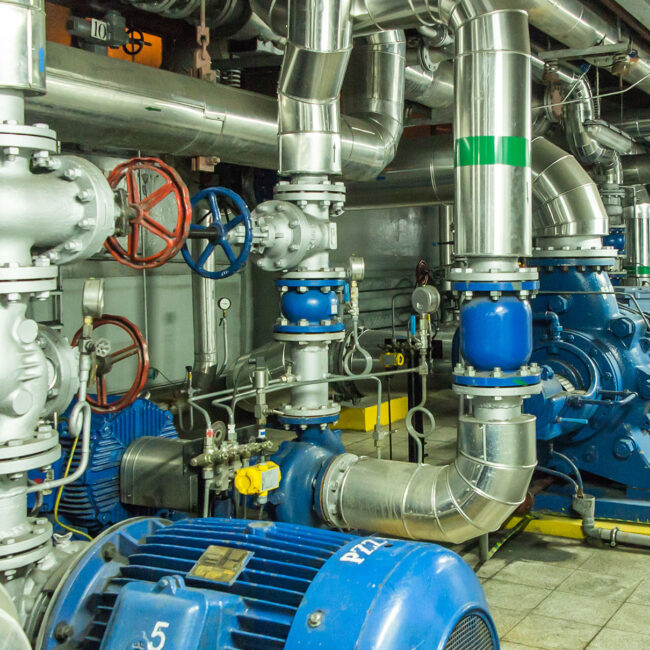
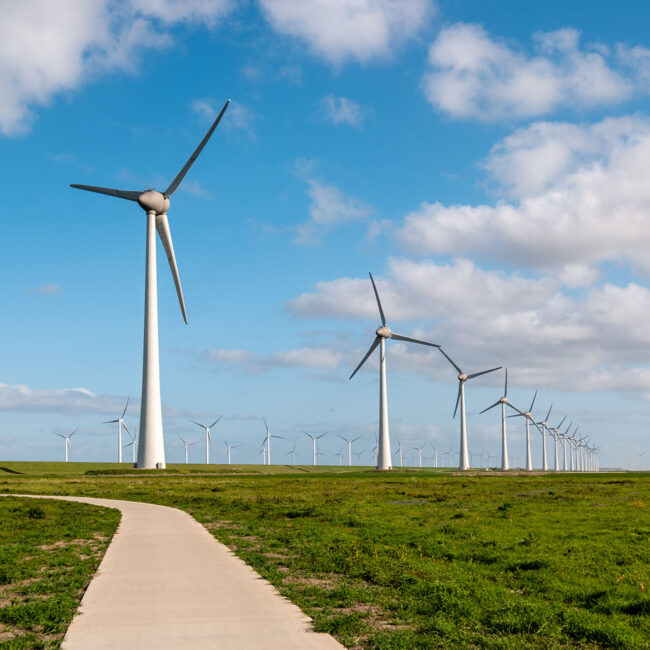
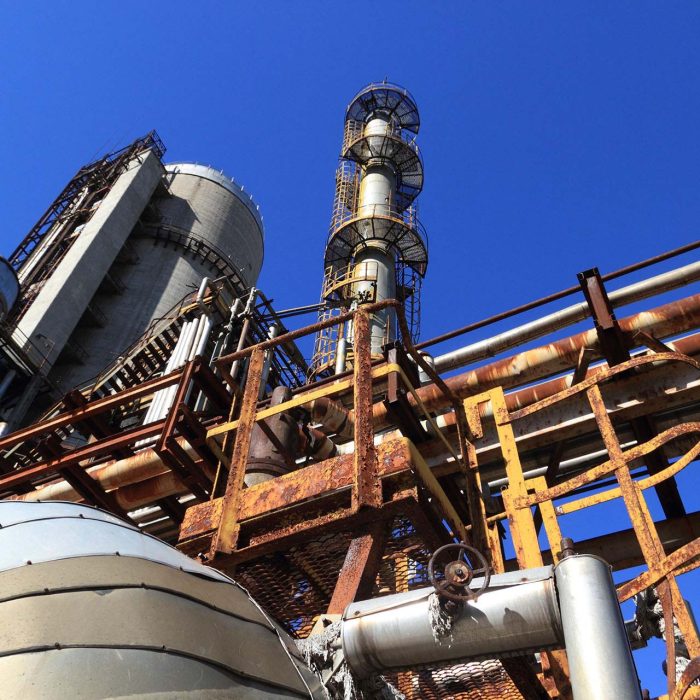
William Blythe:
Stannic Chloride Plant
Problem
Installed in 1998, this Turboscrubber® unit treats the exhaust gases from various reactors, stills and packaging stations in William Blythe’s Tin Plant Recovery Section at Stannic.
Solution
The unit simultaneously scrubs SnCh vapours, their hydrolysis product HC1, and SnOj precipitate to high efficiencies. It was supplied as a replacement and upgrade for an existing packed column scrubber which was prone to blockage by the precipitated solids. The SnOj precipitate is discharged with the spent scrubbing liquor and its valuable tin content recovered.
Results
Osprey/FTL’s fluidised bed Turboid® technology has shown exceptional ability to simultaneously absorb gases and remove fine dust particles across a wide range of industrial applications. In addition the system’s high mass and heat transfer rates offer considerable reductions in scale and cost for gas cleaning plant. Turboid®’s non-clogging nature permits the use of limestone slurries, trade effluents and biomass as scrubbing media.

Kronos, Leverkusen, Germany:
Process Absorber Retrofit
Problem
Removal of Hydrogen Sulphide from gas streams with significant Carbon Dioxide partial pressures have been severely limited in the efficiency of absorption mass transfer rates, due to the interference between the two components. Kronos needed both an increase in throughput by de-bottlenecking the existing unit which was dynamically limited by its original design, and an improvement in H2S removal to meet tighter downstream waste gas emission limits.
Solution
Kronos in Germany use chelate solution to remove the H2S, with a combination of venturi & mobile bed ball scrubbers. There was no space to add additional balls, nor power available on the fan. No improvements could be made on either the gas or aqueous sides without large capital investments and risk of considerable production down time.
Commissioned by Kronos, FTL/Osprey embarked on a rapid initial study and computer model simulation of the process with a view to optimising and upgrading the absorption process. Once the necessary projections of process manipulation had been presented a full-scale process upgrade on one of their production lines was sanctioned. This involved a fast retrofit under joint supervision of a mobile bed scrubber.
Results
By retrofitting the existing mobile bed to TurboScrubber mode with the patented TurboPak® fluidised bed packing elements, and adjusting the liquid side-operating parameters within the available limits, we achieved the following improvements, achieving production and emissions targets without massive capital and running costs or the upheaval of installing additional production plant:
1. Reduced bed height
2. Massively boosted mass transfer rates
3. Increased tower capacity by up to 100%
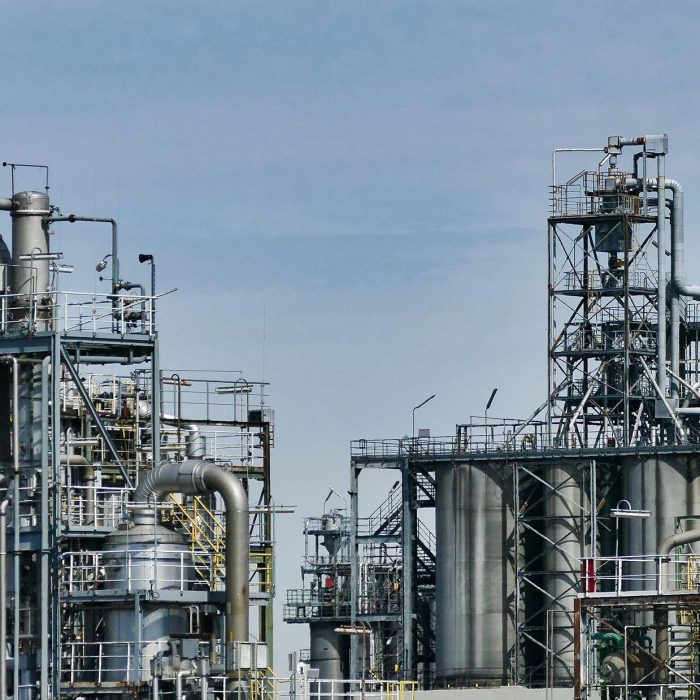
William Blythe UK:
Cl2/ClO2 Absorption
Problem
In 2006 William Blythe requested that FTL/Osprey make an assessment of the suitability of switching and upgrading one of their early TurboScrubber® units. The previous TurboScrubber® unit absorbed H2S to 99.997% efficiency into NaOH to handle Chlorine & Chlorine Di- oxide emissions from process reactors.
Solution
The modelling showed that Cl2 could be scrubbed to very high efficiencies and ClO2 to reasonable efficiencies within the required conditions, and with only minor tower modifications. The chemistry & process of using Na2SO3.xH2O for the absorption & aqueous reaction of Cl2 & ClO2 was incorporated into the FTL/Osprey ScrubMaster® system.
Results
The unit has now been operating successfully for over a decade.