Paper Industries
Success Stories.
What results will I see from Osprey’s products and services? What sort of return on investment can I expect in comparison to other options? How does it work? Our short, easy-read case studies will answer all of those questions and more. We’ve driven real results for our clients in the Paper industries. Find out how we use our approach to make your systems more effective, affordable and sustainable:
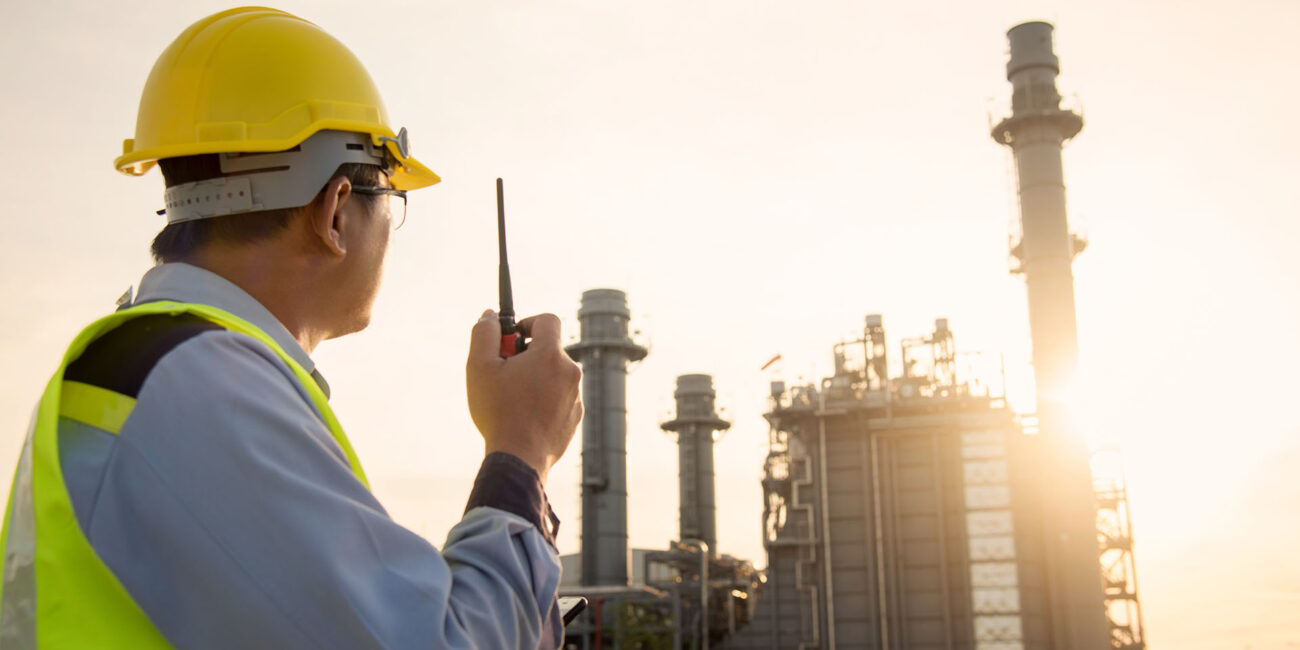
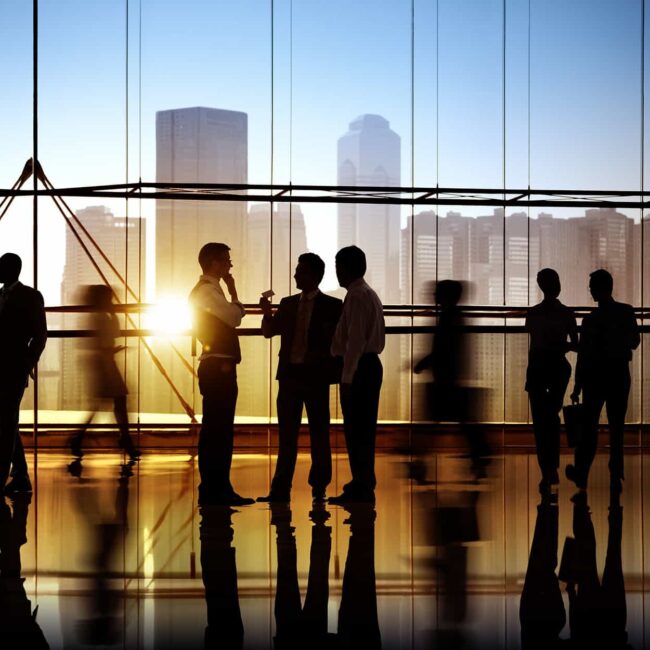
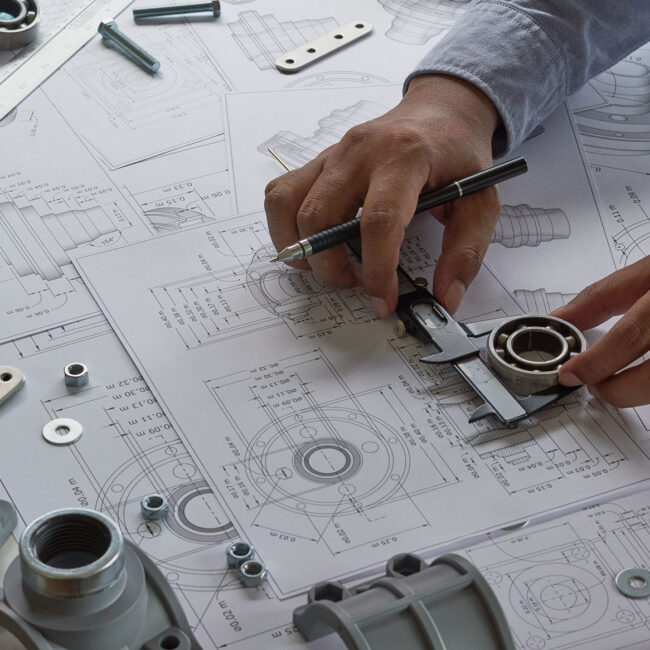
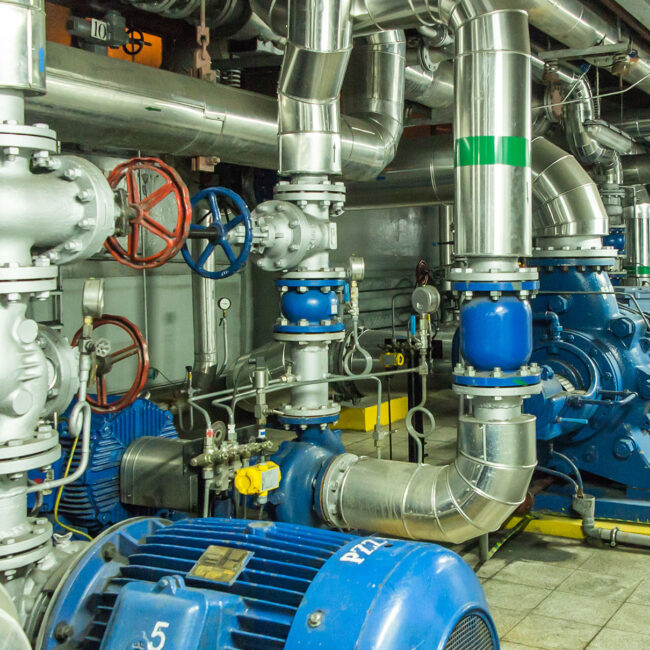
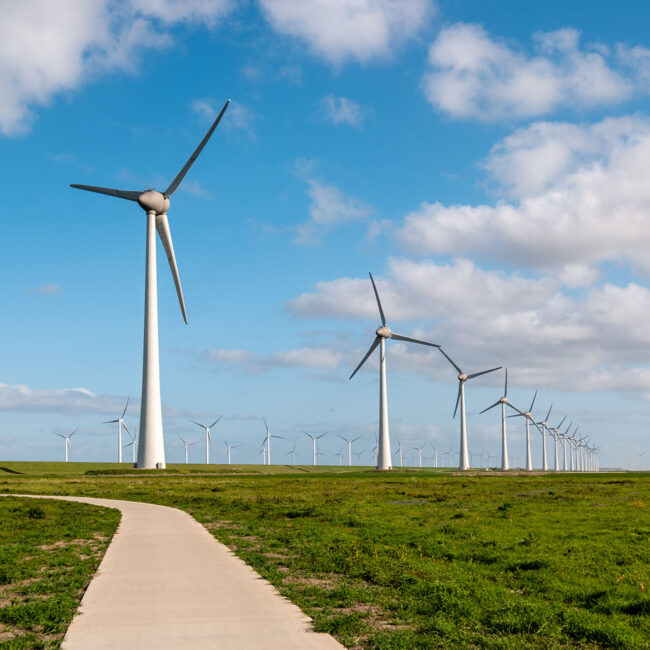
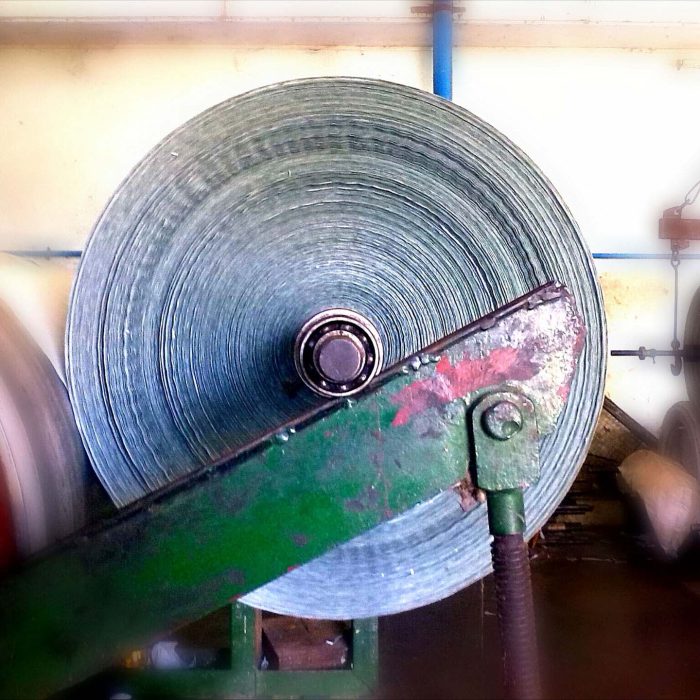
AV Cell, Canada:
SO2 Removal Using Mg(OH)2
Problem
Improving SO2 Removal from AV Cell’s plant in Canada.
Solution
During 2013 a root & branch assessment of the chemistry & process of SO2 absorption using the SO2-HSO3 -SO3 system with an Mg2+ cation in a recirculated slurry fluid bed scrubber was undertaken by FTL/Osprey. This was followed by half year proving trials using our proprietary eccentric Turboid® packings in a tower upgrade to boost SO2 removal performance, minimise constant plugging issues and de-bottleneck the column.
Results
By maintaining SO2 performance with nearly half of the previous pressure drop and maintaining plugging & clogging free operation the old retrofitted Flakt tower is no longer prone to frequent & unexpected shutdowns which previously averaged every 2-3 months. The key to success in such a large tower & complex process is tight pH control to minimise MgSO3.xH2O precipitation, maximise Mg(HSO3)2 product and simultaneously ensure sufficient SO2 absorption to comply with ever tightening emissions limits. The mathematical model developed to allow such tight control was critically augmented by use of Turboid® elements with optimally low bed heights to reduce ∆P, improve flow distribution, eliminate clogging & greatly reduce abrasion.
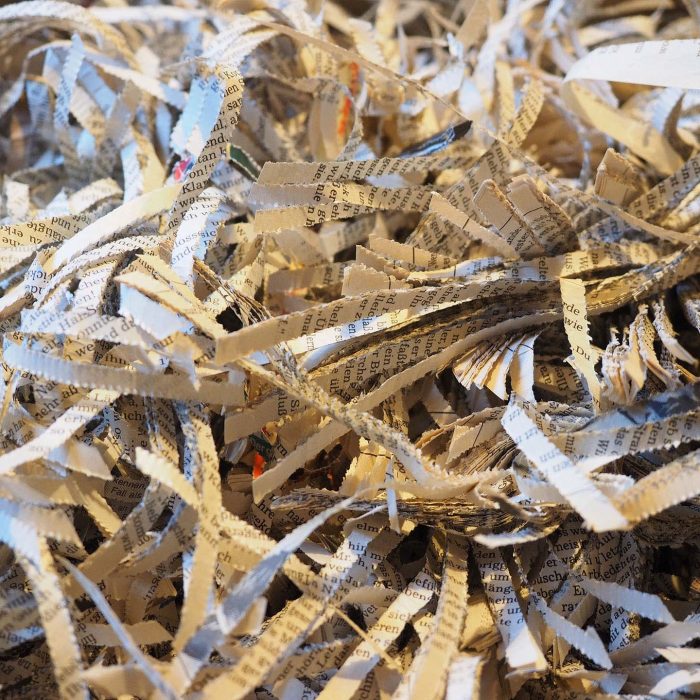
Huhtamaki Pulp & Paper, Maine, U.S.A:
Cooling Process Water
Problem
Cooling process water at Huhtamaki’s Maine pulp & paper facility whilst ensuring continuous non-clogging operation.
Solution
Commissioned in late Spring 2016 this TurbEx® cooling tower cools process water at Huhtamaki’s Maine pulp & paper facility whilst ensuring continuous non-clogging operation even with sticky pulp & solids laden white water. The system is integrated with the plant process control system to ensure optimum operation.
Results
Even operating at low water flow (391USgpm), low enthalpy (water inlet temp only 117oF), high inlet air temp & high RH the heat transfer was still at 3.3MMBtu/hr (~1MW) & the outlet water temp within 3oF of the inlet DB gas temp; equating to a 110 KW/m3K expanded bed HTC. Optimum conditions give ‘Hx’ HTCs > 200KW/m3K.
Wet gas low HTCs shown for Ceramic Intalox Saddles & even Mellapak 250Y structured packing with its 250m-1 interface is only at 10-30KW/m3K.
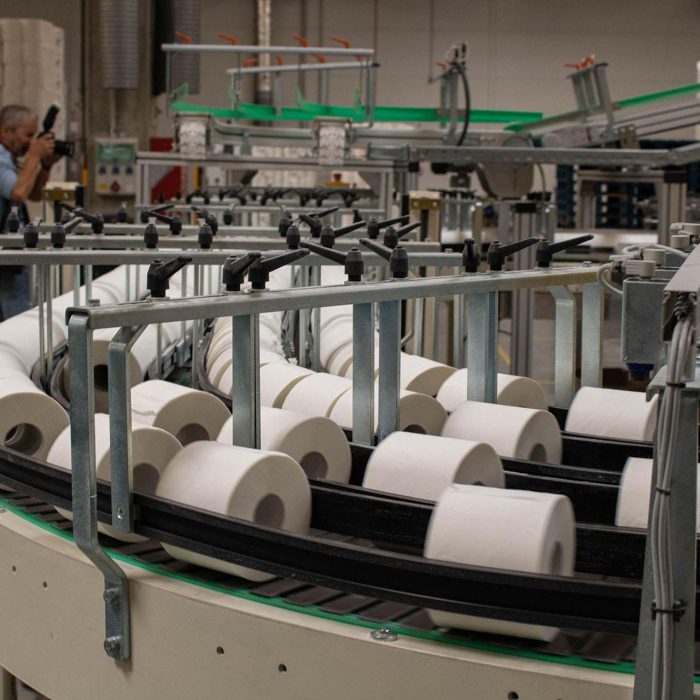
Visy Pulp & Paper, Wagga Wagga, NSW, Australia:
Di-Methyl Sulfide Stripping from White Water
Problem
Removal of organic compounds from process ‘white water’, including Dimethyl-Sulfide, Dimethyl-Disulfide, and Methyl Mercaptan.
Solution
The two Turbostripper® units shown above were installed at Visy Pulp & Paper in 2005 at Wagga Wagga, NSW, Australia, to remove organic compounds from process ‘white water’. The main contaminants of interest were Dimethyl-Sulfide, Dimethyl-Disulfide, and Methyl Mercaptan; which were present in concentrations as high as 10,000 ppb. The TurboStripper’s non- clogging nature permitted the use of the highly contaminated process ‘white water’, a non-homogeneous aqueous concoction of solids and organics
Results
Removal efficiencies of up to 99.99% were achieved. TurboStripper’s non-clogging turbulent fluid bed process is ideal for dealing with such environments, while providing unrivalled mass, heat & particle transfer capabilities.