Waste Management
Success Stories.
What results will I see from Osprey’s products and services? What sort of return on investment can I expect in comparison to other options? How does it work? Our short, easy-read case studies will answer all of those questions and more. We’ve driven real results for our clients in Waste Management industries. Find out how we use our approach to make your systems more effective, affordable and sustainable:
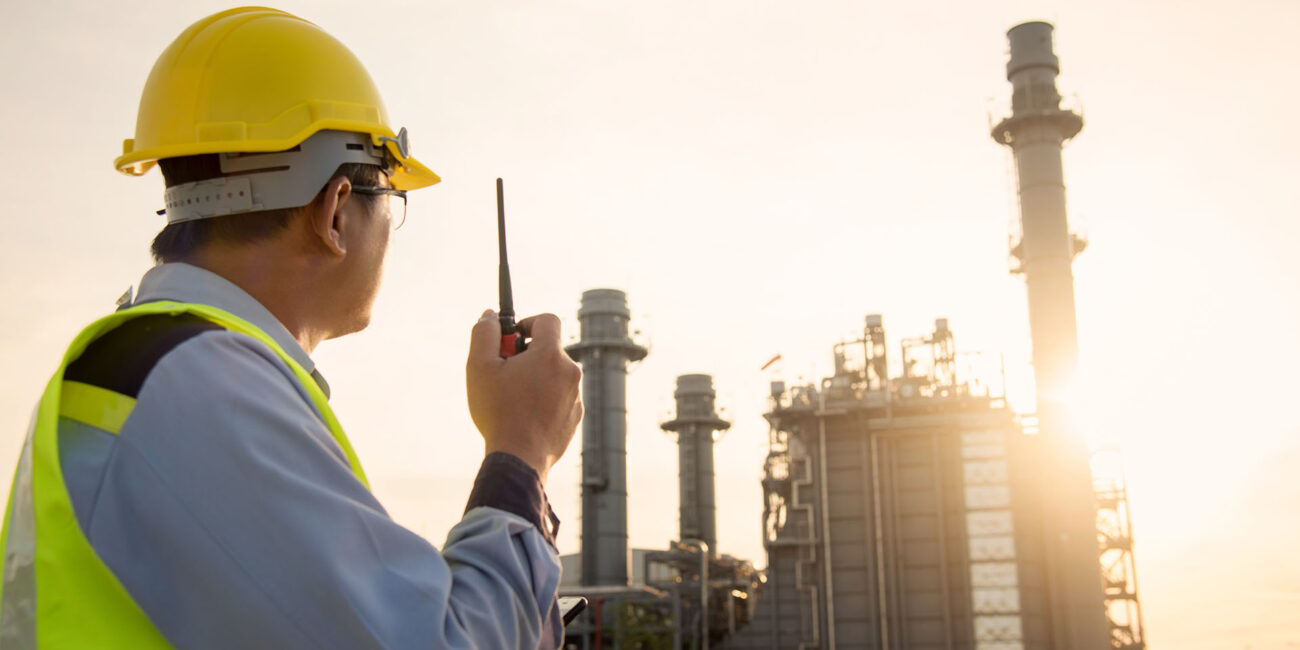
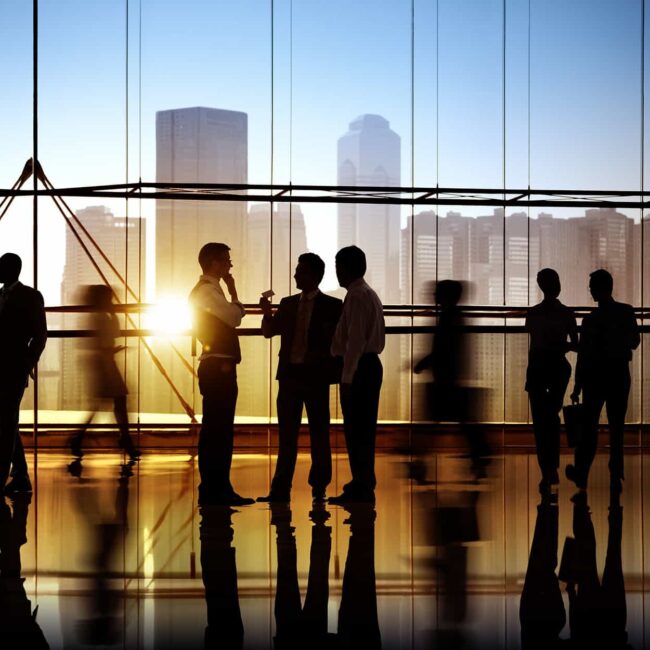
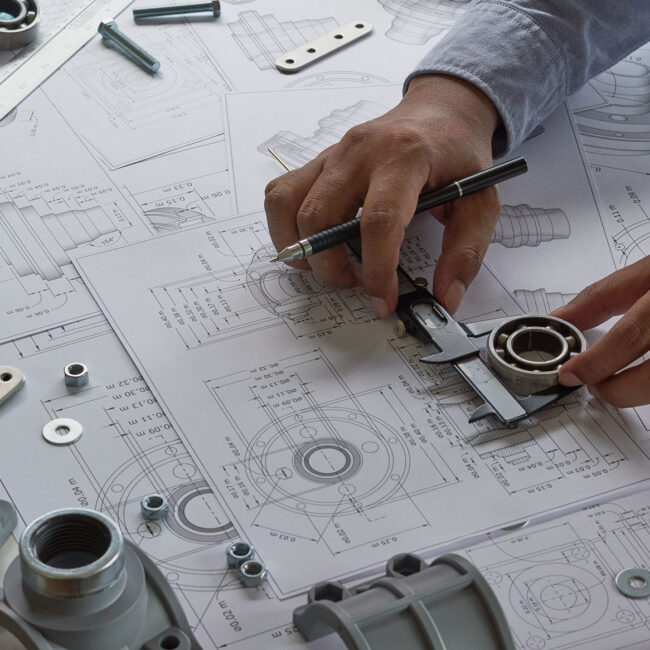
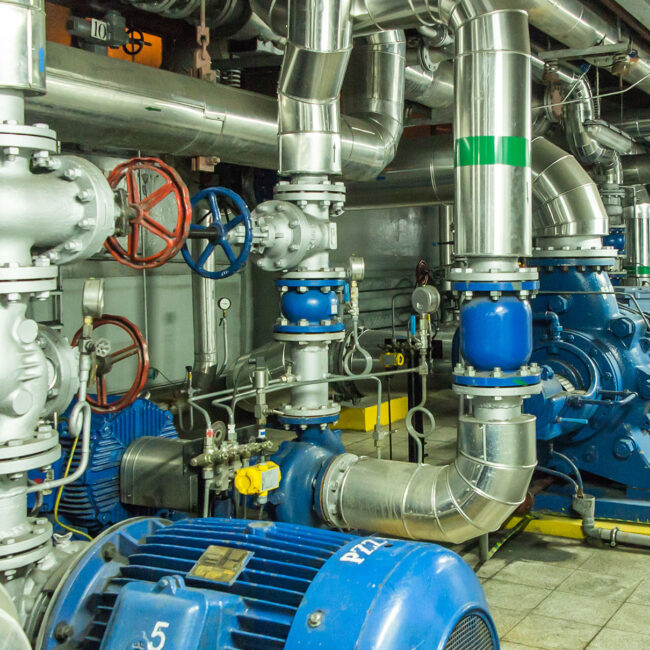
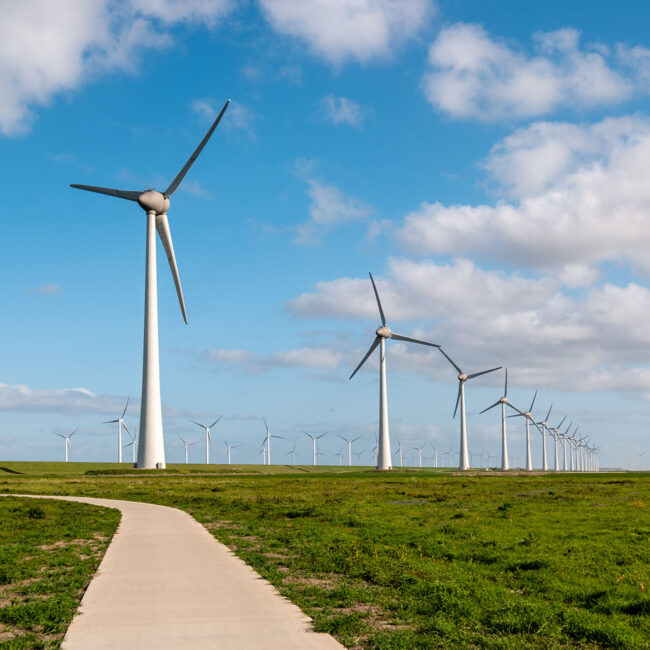
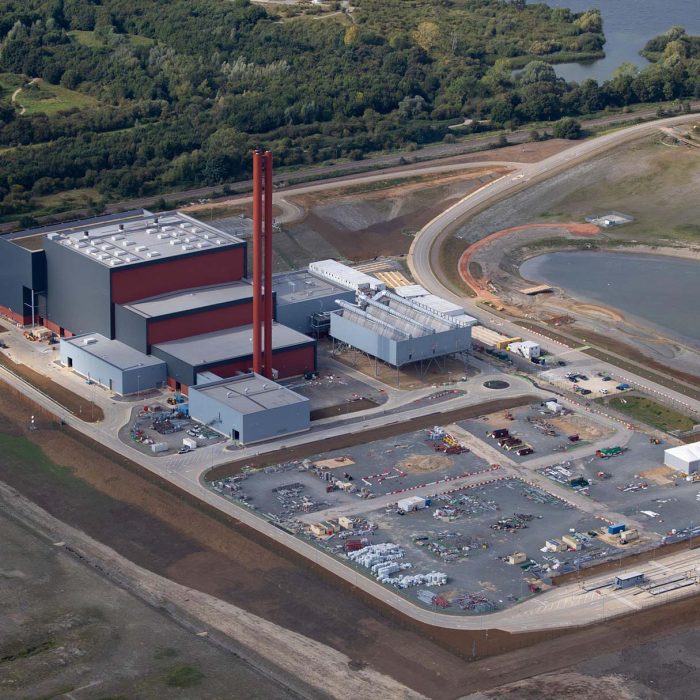
Engelhard:
Metals Recovery Incinerator
Problem
Improving combustion and pollution control at Engelhard’s metal recovery incineration plant.
Solution
The plant was upgraded in 1997 and 1998, a Turboscrubber® system was installed in series with an existing Venturi scrubber. Additionally a sophisticated control system was designed and installed for flexible operation of this versatile plant. Osprey/FTL’s fluidised bed Turbopak® technology has shown exceptional ability to simultaneously absorb gaseous components and remove fine dust and soot particles across a wide range of industrial applications. In addition the system’s high mass and heat transfer rates offer considerable reductions in scale and cost for gas cleaning plant, for example on chemical processes, dryers, boilers and incinerators. Turbopak®’s non-clogging nature permits the use of limestone slurries, trade effluents and biomass as scrubbing media.
Results
A reducing in high fine particulate loadings up to 750 mg/m3 down below 10 mg/m3, better absorption of HCl, and reduced cooling gases for efficient plume suppression.
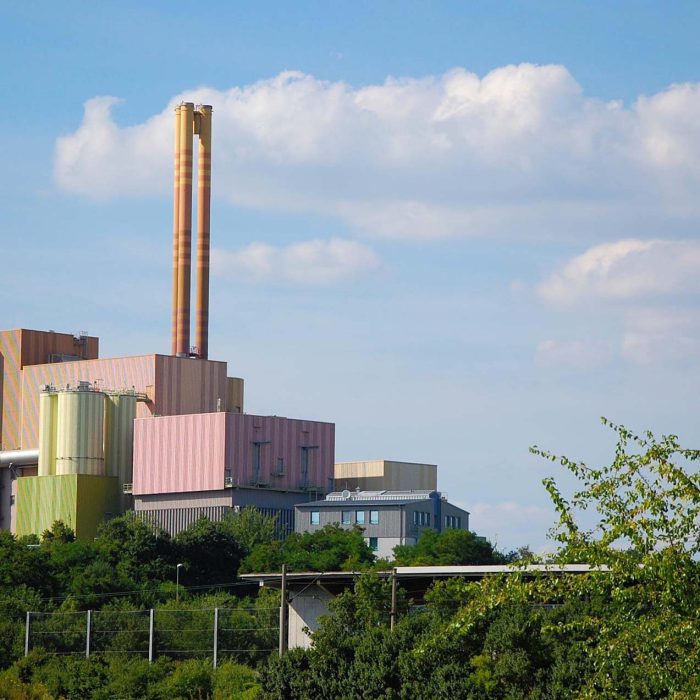
Eli Lilly USA:
High Efficiency Incinerator Scrubber
Problem
How to meet the MACT emission standards at the Eli Lilly plant.
Solution
In 2002 Eli Lilly ordered two TurboScrubber® units from Osprey Corporation installed in series on the outlet of pharmaceutical waste incinerators in Clinton, Indiana. The upstream TS “C/A” unit was for condensing & absorbing of multiple acid gases plus removal of fine particulates using only water & the downstream TS “P/S” or polisher unit was required to perform high efficiency absorption of the cocktail of acid gases using NaOH dosing. Since meeting MACT emission standards was a must for the system & given the very high loadings plant engineers RMT requested the addition of a non absorbing high energy (60” WG) Venturi stage for additional PM removal which could have been handled with far less energy consumption & Capex by increasing the TurboScrubbers’ pressure drops (via L/G & fluid be height increases).
Results
The resultant performance was perfect performance form the improved plant.
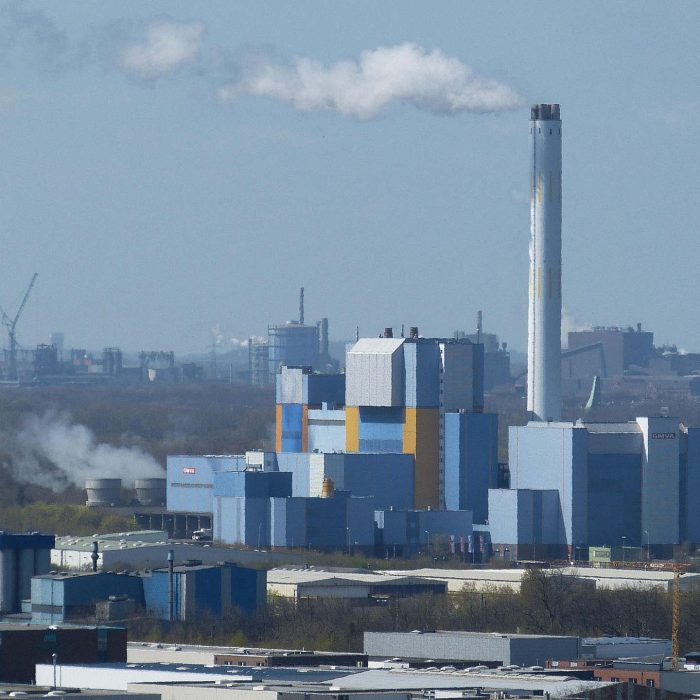
3MW developmental Gasifier in the U.K:
Turnkey Gasification Emissions Control & Effluent Plants
Problem
Installing of our first full scale TurboScrubber® plant on a 3MW developmental Gasifier plant.
Solution
Following many years of pathfinder experience gained installing plants on smaller developmental processes, Osprey/FTL installed its first full scale TurboScrubber® plant on a 3MW developmental Gasifier in the U.K. in 2012-2013. Comprising of two TurboScrubber® units in series with respective cooling and chilling functions, the plant was highly successful in simultaneously removing Condensed Tars, PMs & H2S whilst simultaneously delivering high quality re-heated engine feed Syngas. Absorption enhancing Redox chemistry was chosen to provide favourable selectivity of H2S over CO2 to minimise chemical consumption.
Results
The addition of purpose built oil & tar removal systems with Organic & Inorganic water treatment enables the process to com ply with local authority waste discharge requirements.